How Onsite Services Can Help Businesses Streamline Operations
Pallet management plays a critical role in supply chain efficiency, yet it often operates behind the scenes until inefficiencies begin to affect costs, labor, or delivery timelines. For manufacturers, retailers, and distribution centers, managing pallets in-house can strain internal teams, create unnecessary expenses, and limit operational visibility.
Onsite Services offer a practical solution by embedding trained pallet teams directly within a facility. These teams manage pallet-related tasks in real time — from sorting and repairs to scrap removal and compliance — all tailored to the operational needs of the business.
What Onsite Services Include
Services centralize pallet operations inside the facility, improving visibility and workflow. Core services often include:
-
Sorting of whitewood, pooled, plastic, and other pallet types
-
Onsite pallet repairs and safety stock maintenance
-
Removal and recycling of wood and cardboard scrap
-
Surplus asset tracking and pallet reuse management
-
Dock sweeps, vendor compliance audits, and warehouse support
Many programs also expand to include broader supply chain functions, such as:
-
Return to Vendor (RTV) processing
-
Yard hosteling and freight handling
-
Trailer stripping and salvage dock management
-
Janitorial services
-
Management of captive platforms or totes
This range of services allows businesses to tailor Onsite programs to their operational structure and supply chain complexity.
When Onsite Services Make Sense
The need for Onsite Services often becomes clear when certain patterns emerge, such as:
-
Ongoing purchases of new pallets despite existing reusable inventory
-
Frequent sortation errors or inefficient trailer loading
-
Strained internal labor, especially during peak seasons or disruptions
-
Difficulty meeting sustainability or vendor compliance goals
These signals often point to untapped value in the current pallet program — value that Onsite Services are designed to unlock.
A Strategic Implementation Process
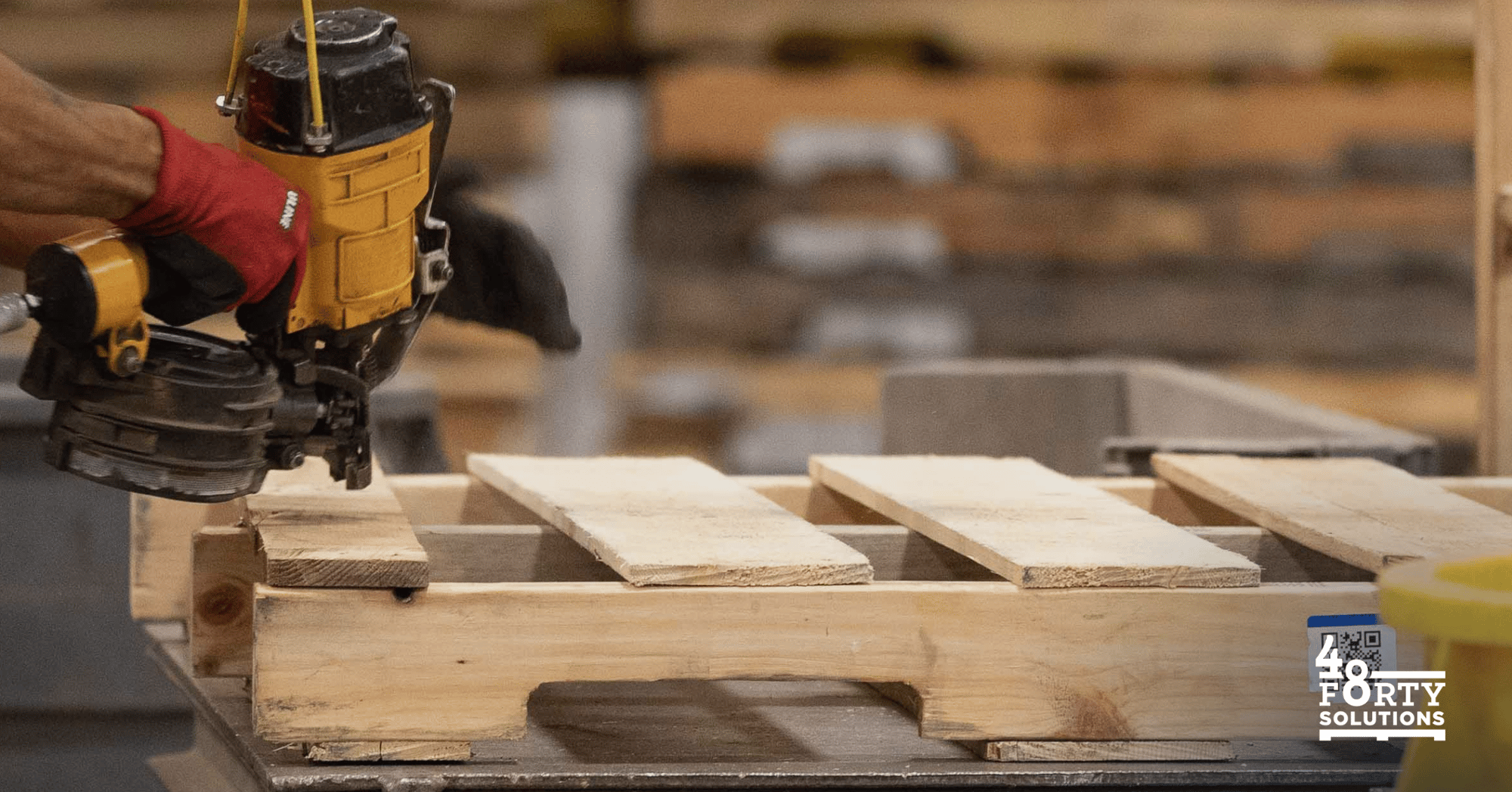
48forty’s approach to Onsite Services begins with a structured discovery process, designed to align services with real-world conditions. The steps typically include:
-
Learn – Site visits to assess facility layout, volumes, hours of operation, and available space
-
Analyze – Recommendations for operational improvements, including workflow adjustments and service scope
-
Implement – Launch of services with defined expectations and timelines
-
Report – Ongoing reporting based on client-specific tracking and visibility needs
This phased process ensures that the program is built around the realities of the facility and delivers measurable results.
Business Benefits of Onsite Services
Cost Savings
By optimizing reuse and sortation of existing pallets, Onsite Services reduce the need for new pallet purchases. Real-time tracking through digital tools gives businesses visibility into pallet flow, load counts, and sort volume across multiple locations.
One national retailer cut millions in pallet expenses after implementing an Onsite program that corrected inefficiencies in their sort process and kept more reusable pallets in circulation.
Process Efficiency
Onsite teams drive improvements across the entire pallet lifecycle. Common enhancements include:
-
Replacing fork-sorting with more efficient hand-sorting
-
Implementing odd-size pallet inspection programs
-
Setting up repair stations to reduce outbound damage or waste
-
Improving trailer load accuracy and turnaround times
These adjustments help reduce operational waste and increase throughput.
Risk Reduction
All Onsite team members are trained to meet the client’s pallet quality and safety standards. Their presence reduces pressure on internal teams and ensures consistency across facilities. This improves overall control, reduces product damage risk, and helps maintain service-level expectations with vendors and customers alike.
The Value of a Full-Service Partner
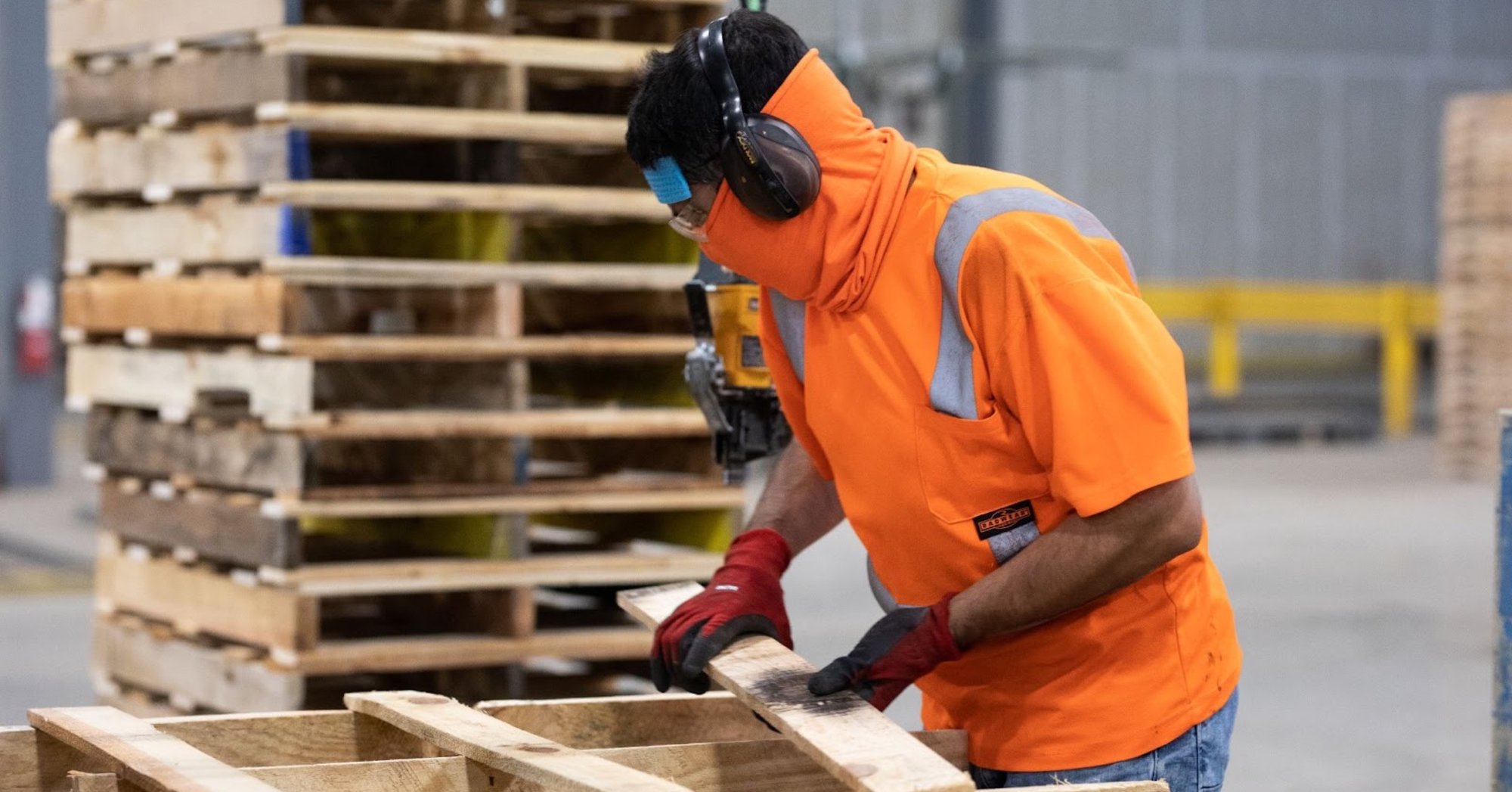
Partnering with an experienced provider streamlines a traditionally fragmented part of supply chain operations. 48forty delivers scalable Onsite Services tailored to each facility’s infrastructure, space, and workflow — whether for a single site or across a national footprint.
From sort programs and sustainability support to comprehensive onsite management, 48forty offers a single, proven solution for better pallet logistics.
Getting Started
As companies continue to seek smarter ways to reduce costs and improve supply chain performance, Onsite Services offer a clear path to operational efficiency. With a focused implementation process and a dedicated team in place, these programs bring structure, savings, and visibility to pallet management in 2025 and beyond.