Complete Guide to National Pallet Management & Logistics
Pallets are the backbone of supply chains – almost literally every product you see in a store or warehouse has spent part of its life on a pallet. In fact, nearly two billion pallets are in circulation across the United States each day, underscoring how essential pallets are for moving goods. For operations managers and logistics professionals, managing this vast pallet ecosystem is a critical task. Effective pallet management means having the right pallets in the right place at the right time, all while controlling costs, maintaining quality, and meeting sustainability goals.
This comprehensive guide to national pallet management & logistics will walk you through everything you need to know about optimizing your pallet program. We’ll explore how pallet solutions – from cost-effective pallet recycling and sustainable pallet programs to custom pallets and onsite pallet management – can streamline your operations. Our focus is on practical, solution-oriented strategies used by industry leaders (like 48forty Solutions, one of North America’s largest pallet suppliers) to help enterprise-level supply chains run smoother. Whether you’re a supply chain director looking to optimize pallet inventory, a sustainability manager aiming to reduce waste with recycled pallets, or a logistics executive seeking a reliable national pallet network, this guide has you covered.
By the end, you’ll understand how to implement end-to-end pallet management practices that improve efficiency, cut costs, and support your company’s objectives. Let’s dive in.
What is Pallet Management & Why It Matters
What is pallet management? Pallet management is the coordinated oversight of all activities involving pallets in your supply chain. In simple terms, pallet management involves the sourcing, maintenance, storage, tracking, and recycling of pallets used by a business. It ensures you always have the pallets you need, in good condition, where and when you need them. This encompasses buying or renting pallets, repairing and recycling used ones, keeping track of pallet inventory across locations, and efficiently moving empty pallets out of your way.
Why does this matter? Because pallets may be low-profile compared to products, but poor pallet management can create high-profile problems. Imagine production lines halted due to pallet shortages, or expensive rush orders for new pallets because too many are damaged or lost. Conversely, a well-run pallet program keeps operations flowing smoothly. Pallet management controls the pallet inventory through services that boost efficiency and ensure a secure supply. When done right, it results in fewer bottlenecks in warehouses, less product damage, and lower supply chain costs.
Moreover, effective pallet management contributes to broader business goals. By maximizing reuse and ensuring pallets are safe and sturdy, companies avoid injuries and downtime. By recycling pallets and using sustainable pallet solutions, they minimize waste and support environmental targets. In fact, efficient pallet management is often called a “linchpin” of supply chain success – it bolsters the bottom line and also improves sustainability, safety, and overall supply chain fluidity.
Key Takeaway: Proper pallet management isn’t just about pallets – it’s about running a safer, greener, and more cost-effective supply chain from the ground up
Challenges in Pallet Management Today
Managing pallets at an enterprise scale comes with its share of challenges. One major hurdle is volatile supply and demand. Pallet availability and prices can swing with the lumber market and economic conditions. For example, natural disasters like hurricanes and fires can disrupt lumber supply, driving up material costs. Regional produce seasons or export booms might create pallet shortages in one area while pallets pile up in another. Industry experts note that there is growing pressure on pallet inventories and pricing when housing construction spikes or other factors strain lumber resources. In short, pallet managers must navigate a market where raw material costs and pallet demand aren’t always predictable.
Another challenge is operational complexity. A company with dozens of distribution centers might be dealing with just as many pallet suppliers and service vendors. Each location might have its own vendor for buying pallets, another for recycling, and different pricing terms. This fragmentation makes it difficult to maintain consistent quality and to get a clear view of your pallet costs and inventory levels. Juggling multiple pallet vendors can lead to inconsistent pricing and quality, and create headaches in tracking pallets across the network.
Space and handling are also constant concerns. Empty pallets can quickly consume valuable warehouse space if not retrieved on time. Conversely, if you under-stock pallets and run out, operations can grind to a halt. Striking the right balance – not too many, not too few – requires careful inventory management (and forecasting peaks like holiday seasons or promotions). Without a dedicated system, companies often end up either hoarding excess pallets “just in case” or scrambling last-minute when supplies run short.
Finally, there’s increasing pressure to improve sustainability and reduce costs in the supply chain. Sending pallets to landfills or constantly buying new ones is both expensive and environmentally unsound. Many organizations are scrutinizing their pallet programs for waste: Are we repairing and reusing pallets as much as possible? Are we optimizing truck loads to avoid shipping half-empty pallet stacks? Without a coordinated pallet strategy, it’s easy to overlook these inefficiencies.
Bottom line: Modern pallet management is a complex puzzle of supply volatility, operational coordination, space management, and sustainability demands. The following sections will show how a strategic approach – often with the help of a national pallet partner – can turn these challenges into opportunities for efficiency.
A map of 48forty Solutions locations across North America (orange dots), highlighting the breadth of its national pallet network.
The Advantage of a National Pallet Network
One of the smartest ways to tackle pallet complexity is by partnering with a provider that offers a national pallet network. Instead of piecing together regional suppliers, a national pallet company can serve all your locations under one umbrella. For instance, 48forty Solutions operates a coast-to-coast network with over 270 facilities across North America. With such reach, they can supply pallets to virtually any of your plants or distribution centers and even rebalance pallet inventory between regions when you have surpluses in one area and deficits in another.
The benefits of a unified, nationwide approach are significant. First, you get consistent quality and service levels everywhere. A company like 48forty owns and operates its pallet plants and fleet (rather than a loose alliance of subcontractors), which means they enforce the same repair standards and grading criteria at every site. You’re not gambling on different vendors doing things differently – your pallets meet the same specifications whether they’re coming from California or North Carolina. Pricing is standardized too: volume purchasing and network efficiencies translate into more stable, often lower, costs. Customers don’t have to negotiate separate deals in each region; you get one contract, one invoice, and one point of contact for all your pallet needs.
Second, a national pallet partner simplifies your logistics. They can provide just-in-time delivery of pallets, so you don’t need to stockpile months’ worth of pallets on your floor. When you’re done with pallets, the same partner will retrieve and recycle them, closing the loop. Top providers even have their own trucking fleet, avoiding third-party transport delays. The result is a more streamlined pallet supply chain: fewer emergency pallet shortages, fewer idle stacks taking up space, and full transparency into where your pallets are. Many companies find that this consolidation frees up internal resources – your staff spend less time managing pallets and more time on core operations.
Finally, working with a national network brings strategic insights. Because they handle so many locations and industries, they can advise on best practices and forecast market trends. For example, your pallet provider can alert you to looming lumber price hikes or suggest alternative pallet strategies during a regional shortage. It’s like adding an expert extension to your team. As 48forty puts it, their nationwide footprint allows them to “bring all those resources to the table” to help customers plan around market volatility. In other words, you gain a partner who is invested in your success at a macro level, not just a local supplier filling orders.
Big Picture: A national pallet network offers scalability, consistency, and simplicity – truly national capabilities with local know-how. You get reliable pallet supply everywhere you operate, unified standards and reporting, and expert support. In short, a national partner can turn pallet management from a headache into a competitive advantage.
Sustainable Pallet Solutions: Recycling & Reuse
Sustainability is a key driver in modern supply chains, and pallet management offers a huge opportunity to boost your green credentials while saving money. The cornerstone of sustainable pallet solutions is pallet recycling – repairing and reusing pallets as many times as possible. Wooden pallets are remarkably reusable; in some cases, a pallet can make up to 15 trips through the supply chain before it’s beyond repair. That is the case with whitewood pallets. By implementing a cost-effective pallet recycling program, companies can dramatically cut down on the number of new pallets they need to buy. In fact, an effective repair-and-return program can greatly reduce costs by extending the life of pallets and preventing new purchases.
The process is straightforward: when pallets come back from the field, they are inspected and sorted. Damaged pallets get repaired – broken boards replaced, weak stringers reinforced – and then the pallet is returned to service. Over multiple cycles, a single pallet might carry many loads for you, delivering far more value than a one-and-done use. Eventually, when a pallet truly reaches end-of-life, it doesn’t head to the dump. Instead, it’s typically recycled into mulch or biomass for fuel. In this way, every part of the pallet finds a second life. This circular approach means far less wood waste and a much lower environmental footprint for your packaging.
Using recycled pallets also directly supports corporate sustainability goals. Every recycled pallet used is one less new pallet that must be built from fresh lumber. That translates to fewer trees harvested and less energy expended on sawmill operations. It helps that North America practices sustainable forestry – the wood used for pallets comes from well-managed forests, and overall, tree stocks have actually grown over the past century. Many companies now prefer recycled over new pallets for both cost and eco-reasons. Recent industry surveys show 71% of companies purchase recycled wood pallets as part of their pallet mix. These pallets offer a cost-effective and environmentally friendly alternative to new ones, and are typically refurbished to meet the same quality standards as new pallets – so you don’t sacrifice performance by choosing green options.
Leading pallet providers make sustainability a core part of their service. For example, 48forty Solutions is the largest pallet recycler in North America, handling over 500 million pallets annually through its recycling facilities. They track every board and nail, aiming to maximize reuse. They’ve even achieved certifications like SFI for responsible sourcing in their operations. By partnering with such a provider, you gain access to sustainable pallet programs that dramatically reduce landfill waste and contribute to your company’s ESG targets.
Takeaway: Pallet recycling isn’t just good for the planet – it’s good for business. Reusing pallets lowers your costs per use and ensures that materials are fully utilized. A well-run pallet recycling program means you’re continuously turning old pallets into like-new resources, creating a win-win for your bottom line and the environment.
Pallet Supply, Retrieval & Logistics Services
Having the right number of pallets when and where you need them is the foundation of pallet management. That’s why many companies invest in professional pallet supply and retrieval services. In a supply & retrieval program, your pallet provider takes on the responsibility of delivering pallets to your facilities (supply) and picking up empty or excess pallets from your facilities or customers (retrieval). The goal is to keep your operations stocked with pallets without overburdening you with piles of empties.
On the supply side, a good pallet partner will work with you to forecast demand and schedule just-in-time pallet deliveries. For example, instead of ordering thousands of pallets weeks in advance and dedicating warehouse space to store them, you can arrange for smaller, regular deliveries that arrive as needed (Pallet Solutions | 48forty Solutions). This reduces onsite clutter and ensures fresh, ready-to-use pallets are always on hand. If your business has seasonal spikes (say, a big holiday push or a quarterly production surge), the supplier scales up deliveries accordingly. And during slower periods, you’re not stuck holding excess inventory.
Retrieval is the flip side of the coin – and just as important. Once pallets have been used for shipping, they often accumulate at distribution centers, stores, or end customers. Rather than letting those used pallets go to waste or become someone else’s problem, a retrieval service brings them back into your supply chain. Providers like 48forty coordinate nationwide pallet pickups through their extensive network (including 850+ partner locations) (Pallet Solutions | 48forty Solutions). They will collect your company’s empty pallets from dozens or even hundreds of drop points, saving you the hassle. Recovered pallets are then inspected and either recycled (if damaged) or put back into your usable inventory if still in good shape.
This closed-loop system has multiple benefits. First, it reduces waste – you’re not throwing away pallets after a single use. Second, it can significantly cut costs. Every pallet retrieved and reused is one less new pallet you need to purchase. In fact, many pallet programs will credit you for surplus pallets: if you have more pallets coming back than you need, the provider may buy them or refurbish and hold them for your future use. Finally, pallet retrieval keeps your facilities (and your customers’ facilities) neater and safer. You won’t have stacks of old pallets creating fire hazards or taking up dock space, because they’re regularly being hauled off by the pallet team.
In terms of logistics, a supply-and-retrieval service essentially outsources the pallet logistics to specialists. They manage the trucking, the scheduling, and the tracking of pallet movements so you don’t have to. Modern pallet companies use online platforms to make this easy – you can place orders for pallets or request a pickup of empties through a web portal or app. For example, 48forty’s PalTrax online system enables customers to schedule services and view reports in real-time. With this visibility, you always know how many pallets are in circulation and can optimize your inventory accordingly.
In Summary: Pallet supply and retrieval programs ensure you always have a steady flow of pallets coming in to support production, and an efficient way to get pallets out once they’ve served their purpose. It’s about maintaining balance – never too few pallets, never too many – while letting experts handle the heavy lifting of pallet logistics.
New & Custom Pallet Solutions for Unique Needs
While recycled 48×40 pallets are the workhorse of most pallet programs, they aren’t one-size-fits-all. Many industries have unique pallet requirements – and that’s where new and custom pallets come in. Perhaps you have a product that’s oversized, oddly shaped, or extremely heavy. Or you’re shipping internationally and need pallets that meet export regulations (like ISPM-15 heat treatment). In these cases, you may need a pallet built to specifications that standard recycled pallets can’t fulfill. A quality pallet provider will offer new pallet manufacturing and custom pallet design services to handle these situations.
Custom pallets are tailored to your specific needs that standard sizes can’t address. The process usually starts with a detailed consultation. The pallet experts will gather information about your use case – What product is going on the pallet? How is it stored and moved (forklift, pallet jack, conveyor)? What are the dimensions of the load and the weight distribution? They might discover, for example, that you need an extra inch of pallet width to prevent product overhang, or thicker deck boards to support a particularly heavy load. “We ask questions like: What product is on the pallet? How is it being moved? Maybe they need an extra inch to avoid damage, or the pallet needs to handle multiple movements. Our expertise helps us design for these exact needs,” says Andy Farris, a regional manager at 48forty. By understanding the details of your operation, they can engineer a pallet that perfectly fits the task.
Once the design is outlined, the provider will typically create sample pallets for testing. They’ll let you try the custom pallet in real-world conditions – load it up with your product, put it through your warehouse handling, even send it through a shipment cycle. This testing phase is crucial to ensure the pallet meets your expectations for strength and handling. Any adjustments (maybe a stronger block here, or a chamfer there to work with your equipment) can be made before full production. The end result is a pallet built to optimize your supply chain: it protects your product better (reducing damage), improves handling efficiency (since it’s designed for your equipment and racks), and can even save space (by fitting containers or trailers more optimally).
Of course, custom pallets often cost more per unit than standard pallets – they may use more lumber or special hardware, and they aren’t produced in the same high volumes. However, businesses find that the investment pays off. With fewer product injuries (and thus fewer product write-offs), smoother loading and unloading, and potentially better cube utilization in transport, custom pallet solutions often lower overall costs over time. It’s a classic case of spending a bit more upfront to save much more down the line. And when you partner with a national pallet supplier, you can get these custom pallets delivered wherever you need them. 48forty, for instance, can produce new and custom-sized pallets at plants around the country and will work with you to determine “the most cost-effective pallet that meets your specifications”.
Pro Tip: Evaluate your operations for any “pain points” that might be solved with a custom pallet. If pallets are breaking too often, or if loads are overhanging, or if you’re shipping air due to a poor fit, a tailored pallet design could drive significant improvements in safety and efficiency.
Onsite Pallet Management Programs
For very high-volume operations, an onsite pallet management program can be a game-changer. In this model – often called Total Pallet Management (TPM) – the pallet service provider actually stations a team at your facility (or dedicates a nearby facility) to handle all pallet-related tasks on the spot. This goes beyond delivering and picking up pallets; it’s an integrated service where experts manage your pallet flow inside your operation.
What does onsite pallet management include? Typically, a crew will sort and inspect pallets as they come off trucks or out of production. Usable pallets are quickly put back into circulation for your loading needs, while damaged ones are pulled aside for repair. Minor repairs (like replacing a broken board) might be done right there onsite, so the pallet can be reused immediately. The team often handles “sharking,” which means roaming the facility to collect stray pallets and keep work areas clear. They’ll manage a pallet inventory onsite, ensuring there’s always a buffer of good pallets ready for use, and preventing piles of excess pallets from building up.
Onsite services can also extend to related tasks. For instance, 48forty’s onsite programs for retail customers include labor to process return trailers, handle freight sortation, and even perform some recycling and janitorial tasks as needed. The idea is to take all the pallet and packaging burden off your staff. Instead of your warehouse workers spending time sorting pallets or loading scrap trailers, the onsite pallet team takes care of it. They coordinate outbound shipments of scrap wood or excess pallets, and they prepare pallets for reuse within the facility.
The benefits of an onsite pallet program are significant. Efficiency jumps, because your employees focus on their primary jobs (like picking orders or loading trucks) while pallet specialists keep the material handling infrastructure (the pallets) in smooth working order. Cost savings often follow – with onsite repair and reuse, you get more life out of each pallet and cut down on off-site trucking. One case study found that implementing an onsite pallet sort and repair program reduced per-pallet costs by around 25% at each site, thanks to reusing pallets that would otherwise have been discarded. Safety and housekeeping improve too: fewer pallets lying around means fewer trip hazards and a tidier operation overall.
Perhaps most importantly, onsite management provides real-time responsiveness. If a particular load of incoming pallets is below quality standards, the onsite team catches it and corrects it (by fixing or discarding) before it causes a problem in your process. If you suddenly need an extra 500 pallets today, the onsite manager can pull from reserve stock or arrange an emergency shipment immediately. Essentially, it’s like having a pallet department in-house, but run by experts and scaled to your needs. It’s no surprise that big-box retailers and manufacturers often use this model – 48forty’s affiliated company, Relogistics, runs onsite pallet programs at over 170 retail distribution centers across the country.
Insight: If your facility deals with thousands of pallets a week, consider an onsite pallet management solution. It can drive down costs per pallet, improve safety, and allow your team to focus on what they do best while pallet pros handle the rest.
Pallet Pooling Services vs. Pallet Programs
No discussion of pallet management is complete without mentioning pallet pooling. Pallet pooling services (offered by companies like CHEP, PECO, or iGPS) provide a rental model for pallets: you essentially rent pallets per trip rather than owning them. In a pooling model, the pool provider owns a large fleet of standardized pallets (often painted or RFID-tagged for tracking). You get pallets from the pool for your shipments and at the end of the supply chain, the pool company retrieves them, inspects/repairs them, and recirculates them to the next user. It’s a bit like leasing a car versus buying – you pay per use and let the owner worry about maintenance and end-of-life.
Pooling has some clear advantages. For one, you don’t have to invest capital in buying pallets (and then worry about depreciation or loss). There’s no upfront cost – you pay as you go, which can be attractive for cash flow. The pooling provider guarantees consistent pallet quality; for example, CHEP’s blue pallets are built to exacting specs and regularly repaired, so you know each pallet will perform reliably. And importantly, they handle reverse logistics on a broad scale. If you ship products to hundreds of different customers, collecting your own pallets can be impractical – but a pooling service will have recovery systems in place (since many other companies are also returning those pooled pallets). This can spare you the headache of chasing empty pallets across the country.
However, pallet pooling isn’t necessarily the best fit for every scenario. The rental fees and loss charges can add up. Over time, the per-trip cost of pooling might be higher than the cost of owning and reusing a pallet if you have an efficient program. It often comes down to your network. If you ship mostly to locations where you can easily get your pallets back (or where your pallet provider, like 48forty, can retrieve them for you as part of a program), then running your own pallet program with recycled pallets could save money. On the other hand, if you distribute product widely to third parties (e.g. consumer goods going to thousands of retail outlets), pooling can simplify operations – which is why many manufacturers in the grocery and beverage sector use pooled pallets by default.
Some companies even use a hybrid approach: they might use pooled pallets for specific customers or lanes that demand them, and use their own pallets (managed through a recycling program) for other flows. There’s no one-size-fits-all answer. The key is to analyze the total costs and benefits. A reputable pallet partner can help with this analysis – for example, 48forty’s team often consults on whether a customer is better off continuing with rented pallets or switching more volume to a recycled pallet program. In either case, 48forty can assist (they routinely sort and return pooled pallets like CHEP and PECO as part of onsite services for clients). The ultimate goal is to ensure you have the right pallet solution for each part of your supply chain.
Should You Rent or Own Pallets?
In short, it depends on your distribution pattern and cost structure. Pallet pooling services offer convenience and guaranteed quality, but managing your own pallet fleet can be more cost-effective and flexible if you have the means to recapture and reuse pallets. Many large operations find value in both – leveraging pool pallets where they make sense, and running in-house pallet programs elsewhere.
Optimizing Pallet Inventory & Tracking
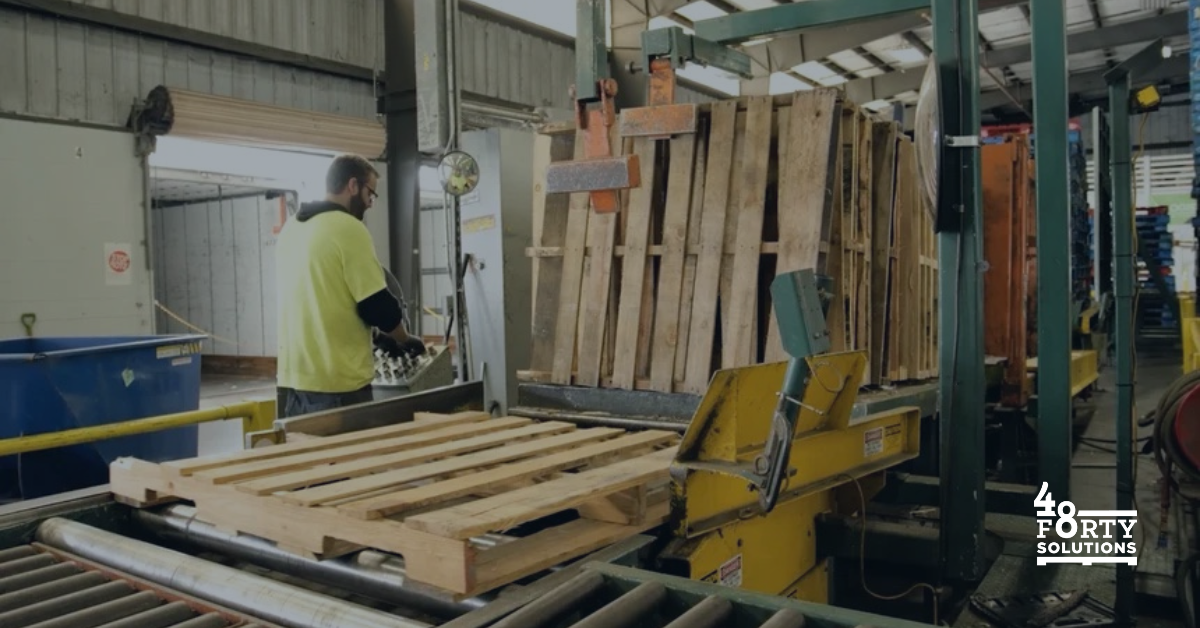
How do you know if you have the “right” number of pallets in your system? Too few, and you risk production downtime; too many, and you’re tying up capital and space. Optimizing pallet inventory is a continual balancing act, and it’s an area where data is your friend. Leading pallet management programs use tracking tools and analytics to monitor pallet flows and adjust inventory levels in real-time.
Start with visibility. You can’t optimize what you don’t measure. By implementing a tracking system – even something as simple as regular inventory audits at each location, or as advanced as RFID-tagged pallets scanned through each transfer – you gather the data needed to manage your pallet pool. Most national providers supply inventory reports as part of their service. For instance, 48forty’s online PalTrax portal gives customers on-demand insight into pallet orders, deliveries, pickups, and balances across all their sites. With centralized tracking, you can see at a glance where your pallets are. If one warehouse is accumulating a surplus, you can divert deliveries to another location or schedule a transfer. If another site is consistently running short, you’ll spot the trend early and increase its par level of pallets.
Analytics also help in forecasting. Pallet usage often correlates with production or sales volume, which means your historical data can predict future needs. By analyzing seasonal patterns or sales forecasts, you and your pallet provider can plan inventory requirements in advance (avoiding last-minute scrambles). Modern pallet management is starting to incorporate IoT sensors and advanced software for even finer control – but even basic data like weekly pallet throughput by site is extremely useful.
Another aspect of optimization is vendor-managed inventory (VMI) for pallets. Some companies effectively outsource the monitoring of pallet stock to their pallet vendor. In this arrangement, the pallet provider tracks how many pallets you have and automatically replenishes or removes pallets to maintain agreed-upon levels. This takes the guesswork off your plate entirely. It’s similar to how suppliers manage refillable packaging in a just-in-time manufacturing environment. The result is that you always have an optimal buffer of pallets without manually placing orders all the time.
Of course, optimization isn’t only about counts – it’s also about quality. Tracking systems should note the condition of pallets, so that damaged ones are removed and replaced promptly. Key performance indicators (KPIs) like pallet rejection rate, repair turnaround time, and loss rate can be used to gauge how well the pallet inventory is being maintained. Top providers often share such metrics in regular reports, giving you full transparency. This transparency builds trust and helps identify areas for improvement (for example, if one plant is losing pallets at a higher rate, you can investigate why – maybe drivers aren’t exchanging them properly at that location).
In short, optimizing pallet inventory comes down to visibility and proactive management. By leveraging technology and the expertise of your pallet partner, you ensure that your pallet supply is right-sized and ready to support your operations at all times. No more pallet pile-ups, and no more pallet shortages – just a smooth, data-driven flow.
Choosing the Right Pallet Supplier
With all these considerations in mind, how do you select the best pallet supplier or partner for your organization? Here are some key factors and questions to guide your decision:
- Capabilities & Network: Assess whether the supplier can support all your locations and needs. Do they have a national pallet network if you operate across multiple regions? A provider with many facilities (and partner depots) will be more likely to meet surges in demand and reposition pallets as needed. For example, 48forty’s network of 270+ facilities and 850 partners gives it unrivaled reach. Ensure they can provide new pallets, recycled pallets, custom builds, onsite services – the full suite of pallet solutions you might require as your business grows or changes.
- Experience & Reputation: Look for demonstrated expertise. How long have they been in the industry, and who are their customers? A solid track record – such as being trusted by close to 4,000 customers across a wide variety of industries – indicates reliability. Don’t hesitate to ask for case studies or references relevant to your sector (e.g., do they have experience with food & beverage supply chains, or retail distribution, or whatever niche you’re in?).
- Quality Standards: Pallets might seem simple, but quality can make or break your operations (literally, if a pallet fails). Inquire about the supplier’s quality control processes. Do they have a formal Quality Management System with regular audits? Top companies implement programs with standardized inspections, repair criteria, and even use protocols like Good Manufacturing Practices (GMP) at their facilities. Also, what grades of pallets do they offer and how do they ensure consistency in grading? A reputable supplier will be transparent about their grading definitions and have no issue providing you with spec sheets.
- Transparency & Reporting: In modern supply chain partnerships, data sharing is crucial. The right pallet partner should offer clear reporting on deliveries, pickups, inventory levels, and costs. Ideally, they provide an online portal or regular reports (monthly, quarterly) that let you track your pallet program’s performance. Look for those who emphasize transparency – for instance, delivering digital proof of delivery and detailed usage reports – so you’re never in the dark about the status of your pallets.
- Sustainability Practices: Your pallet supplier should help advance your sustainability goals, not hinder them. Discuss their green initiatives: Do they refurbish and reuse pallets extensively? What percentage of pallets in their pool are recycled vs. new? Do they recycle scrap wood into mulch or energy? Have they invested in eco-certifications or carbon reduction efforts? Choosing a supplier committed to sustainable pallet solutions, like 48forty’s leadership in recycling and environmental monitoring, can bolster your own environmental commitments.
- Cost-Effectiveness: Notice that we didn’t list price first – that’s deliberate. While cost is important, focus on total value rather than just the lowest unit price per pallet. The cheapest pallet supplier might cut corners that cost you more in product damage or unreliable supply. Instead, evaluate the overall ROI of their pallet program proposal. How do they plan to reduce your hidden costs (like disposal fees, labor time managing pallets, or freight on empty pallets)? A good supplier will perform an analysis and identify areas to save you money, not just sell you pallets. Compare pricing structures too – some work on per-pallet purchase, others on per-trip rental, others on management fees for an all-inclusive service. Make sure you’re comparing apples to apples.
- Customer Service & Flexibility: Finally, gauge the intangible factors. How responsive is the supplier in communication? Are they willing to customize a pallet program for you, or are they pushing a one-size-fits-all package? Your pallet needs may evolve (new distribution centers, changes in product lines, etc.), so you want a partner that’s flexible and will work with you to adjust the program over time. Strong customer support – e.g., a dedicated account manager you can call in a pinch – is invaluable.
By weighing these factors, you can choose a pallet supplier that truly functions as a strategic partner. The right choice will bring not just pallets, but expertise, efficiency, and peace of mind to your supply chain.
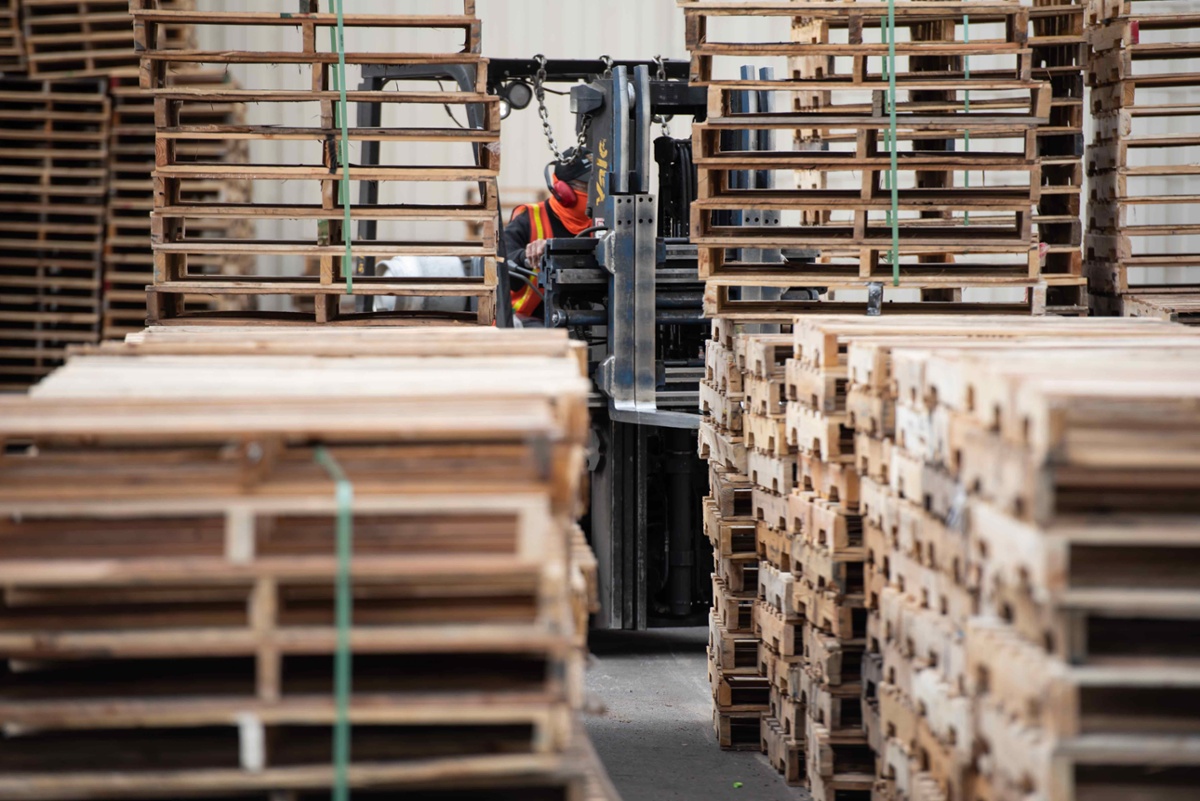
Future Trends in Pallet Management
What does the future hold for pallet management and logistics? While pallets have been around for decades, the industry continues to evolve and adapt to new supply chain realities. Here are a few trends and developments that enterprise shippers and pallet providers are watching:
- Digital Tracking & Smart Pallets: Expect to see more technology embedded in pallet operations. RFID tagging of pallets, once considered too costly, is becoming more feasible as tag prices drop – enabling automatic tracking of pallet movements through warehouses and in transit. Some companies are piloting IoT-enabled pallets with sensors that can report location, temperature, or shock events. Even without smart hardware, software is getting smarter: pallet management systems will integrate with broader supply chain platforms (so pallet availability can be synchronized with production plans, for example). The result will be even greater visibility and proactive control over pallet fleets.
- Automation-Ready Pallets: As warehouses automate (with robotic forklifts, automated storage and retrieval systems, etc.), the demand for pallets with tighter specifications and durability is rising. Automated systems can be picky – a broken board or inconsistent pallet size can stop a high-speed operation. Going forward, pallet suppliers will likely offer premium “automation-grade” pallets designed for these environments, and we may see more plastic or composite pallets used in closed-loop automated settings for their precision and longevity. Pallet management programs will need to accommodate these high-spec pallets (maintaining their quality rigorously) alongside standard pallets.
- Greater Sustainability Commitments: The push for sustainability will only intensify. We can anticipate even higher rates of pallet reuse and recycling (the industry recycling rate is already above 90% and climbing). Carbon footprint tracking might become a standard part of pallet reporting – e.g., your pallet provider might tell you how many trees you saved or how much carbon emission you avoided by using recycled pallets. Also, alternative pallet materials (like presswood, bamboo, or recycled plastic) could gain traction if they prove to have lifecycle benefits. Large companies might set goals for pallet procurement (e.g., 100% of pallets from sustainable sources or 0% landfill waste from pallets), driving innovation in pallet design and end-of-life processing.
- Resilience and Flexibility: The pandemic-era supply chain shocks (including pallet shortages in 2021) taught companies the importance of resilience. In the future, we expect more businesses will formalize their pallet contingency plans – such as maintaining a strategic reserve of pallets or qualifying multiple sources (recycled and new, multiple vendors) to avoid disruptions. Pallet providers are also diversifying and expanding their networks to be more agile when demand spikes. The continued growth and consolidation in the pallet industry (for example, 48forty’s expansion in recent years) indicates that providers are gearing up to service ever-larger customers with nationwide needs. The US pallet market is projected to continue growing steadily (~5–7% annually) through the next decade, resulting in both increased demand and competition.
Integrated Solutions: Finally, pallets won’t be managed in isolation. We’re seeing a trend toward integrated packaging and pallet solutions. Some pallet companies also handle crates, totes, and dunnage, providing a one-stop solution for all reusable transport items. The line between pallet management and overall supply chain consulting is blurring – your pallet partner might also advise on load planning, product packaging improvements, and reverse logistics optimization (since all are intertwined). This holistic approach will further elevate the pallet from a humble wood skid to an important component of strategic supply chain design.
In summary, pallet management is moving toward smarter, greener, and more resilient practices. Operations managers can look forward to better tools and data to manage their pallets, and a continued emphasis on reliability and sustainability from pallet providers. By staying attuned to these trends and working closely with your pallet partners, you can ensure your pallet program remains future-proof and continuously improving.
Conclusion: Building a Resilient Pallet Program
Pallet management may not always get the spotlight in supply chain discussions, but as we’ve seen, it has a profound impact on cost, efficiency, and sustainability. The national pallet management and logistics strategies covered in this guide – from leveraging a vast pallet network, to implementing recycling and onsite solutions, to customizing pallets for optimal performance – all share a common goal: turning your pallet program into a competitive advantage. By treating pallets not as an afterthought, but as a strategic asset, you set the stage for smoother operations and significant savings.
As you move forward, remember that the best pallet programs are built on partnership. Working closely with a qualified pallet provider allows you to continuously improve and adapt your approach. Need to reduce costs? They can help identify recycling opportunities or optimize pallet specs. Facing rapid growth or new markets? They can scale with you, ensuring pallet supply never becomes a bottleneck. The key is to apply the principles from this guide in a way that fits your organization’s unique needs – and to lean on experts who do this day in and day out.
In the end, efficient pallet management is a win-win-win: lower operational costs, higher supply chain reliability, and a smaller environmental footprint. Companies that master it will find that pallets “just work” in the background – supporting the business quietly but effectively. If you’re looking to elevate your pallet program to that level, consider reaching out for professional help. 48forty Solutions, as one of the largest pallet suppliers in the nation, has the experience and infrastructure to design a program tailored to your needs. From sustainable pallet solutions to full pallet pooling programs, they’ve done it all. Feel free to request a quote or consultation to explore what a modern pallet management approach can do for your business.
With the right strategy and the right partner, pallet management isn’t just about moving things – it’s about moving your company forward.